
› I nuovi motori 1.0 TSI della serie EA211 sfruttano un sottile rivestimento al plasma in luogo del precedente riporto in ghisa
› La nuova tecnologia riduce consumi, emissioni e consente di ridurre la massa complessiva del propulsore
› Investiti 28,8 milioni di euro per l’adeguamento del processo produttivo presso l’impianto di Mladá Boleslav
ŠKODA AUTO ha implementato un nuovo processo produttivo che prevede l’utilizzo di un sottile riporto al plasma sui cilindri del nuovo 1.0 TSI EVO.
Questa nuova tecnologia permette di stendere sulle superfici un rivestimento di soli 0,15 mm che riduce gli attriti e di
conseguenza consumi ed emissioni, oltre a contenere il peso del motore. Il nuovo propulsore è prodotto a Mladá Boleslav, dove sono stati investiti 28,8 milioni di euro per la preparazione e la conversione della linea di montaggio.

Così Christian Bleiel, Responsabile Produzione della Componentistica in ŠKODA AUTO: “Il rivestimento al plasma rende i motori EA211 TSI EVO ancora più efficienti. Riduce le perdite per attrito e di conseguenza migliora i consumi. Inoltre, questo rivestimento innovativo permette di
distribuire il calore in modo migliore tra i cilindri e ne consente una migliore dissipazione, riducendo il carico termico. I nuovi motori, prodotti a Mladá Boleslav sono montati su FABIA, SCALA, KAMIQ e KAROQ e sulla variante 1.0 e-TEC mild-hybrid di nuova OCTAVIA.
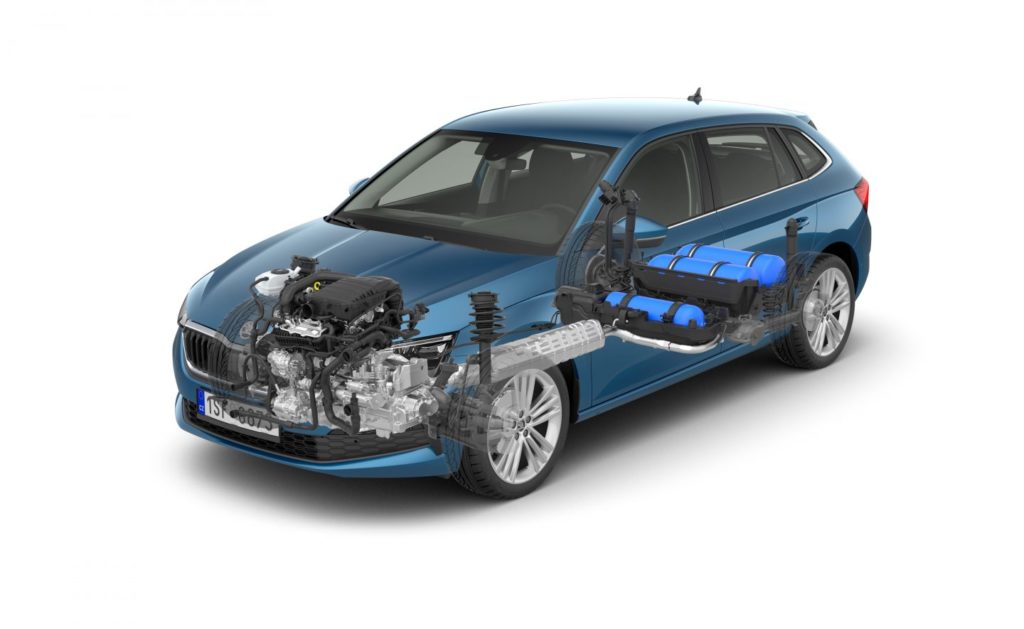
Prodotti su due linee di assemblaggio, i nuovi motori TSI EVO hanno comportato un investimento di quasi 29 milioni di euro, portando a oltre 69 milioni di euro l’investimento complessivo sostenuto da ŠKODA in tempi recenti per la modernizzazione dei propulsori.
Il processo produttivo prevede prima la foratura del blocco cilindri. In seguito, un laser da 1.500 watt abrade la superficie dei cilindri per permettere al rivestimento al plasma di aderire perfettamente. Il fascio di luce crea dieci piccoli incavi per millimetro, con una profondità di circa 40
micron. Questa fase produttiva avviene in atmosfera controllata, satura di azoto per non contaminare il raggio laser e garantire accuratezza.
Successivamente, idrogeno e argon vengono utilizzati per creare il plasma gassoso, impiegando circa 4,5 litri di idrogeno al minuto. Raggiunta una temperatura di circa 15.000° Celsius, il plasma viene poi miscelato con vari tipo di acciaio ridotti in polvere finissima, contenente acciaio, carbonio,
silicio. I singoli granelli hanno un diametro massimo di 50 micron.
Spruzzata sulle superfici dei cilindri, la polvere disciolta dall’altissima temperatura forma un sottile film di circa 250 micron, che viene poi ridotto a 150 micron nella successiva fase di lucidatura. Per fare un confronto, il
rivestimento di un cilindro tradizionale solitamente misura 4 millimetri.
Durante tutto il processo, ogni cilindro viene misurato più volte tramite strumentazioni ottiche per garantire il rispetto degli standard qualitativi, prima di un test finale volto a misurare la resistenza
del rivestimento al plasma.
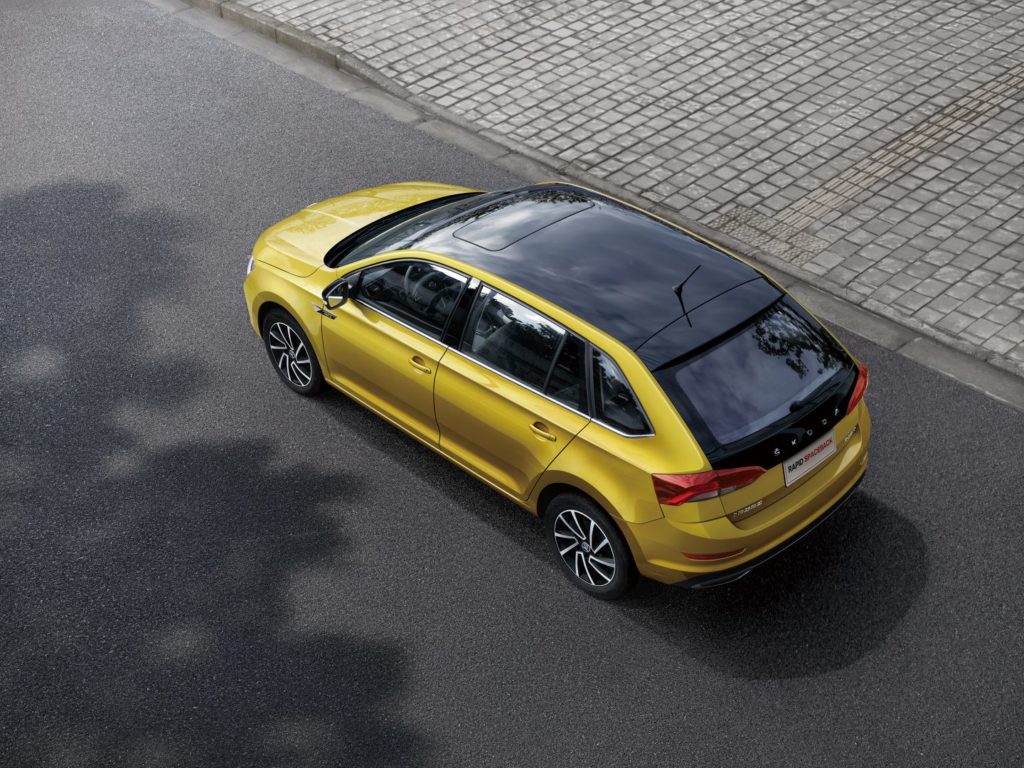
Post simili
Motodays 2025: una terza giornata tra esperienze, passione e grandi numeri
Suzuki Motor Corporation presenta la GSX-8R Tuned by JURI ispirata al videogioco “Street Fighter 6”
Jorge Martin inaugura il prebooking di Aprilia Tuono 457